This article on Robotics with Experimental Modal Analysis written by Damiano Carra, Enrico Sabbatini, and Lorenzo Caraccio from the Polytechnic University of Turin. Original Article
As technology continues to push the boundaries of space exploration, ensuring the reliability of critical components is essential. One such challenge is designing wheels capable of withstanding the harsh Martian environment. The DIANA team, a group of students from Politecnico di Torino, has developed ARDITO, a modular space rover designed to assist astronauts on planetary missions. A key innovation in ARDITO is its airless wheels, designed to provide superior grip and durability on rugged terrain.
To validate the structural integrity and performance of these wheels, the DIANA team partnered with Dewesoft to conduct Experimental Modal Analysis (EMA). This study ensured that the wheels could handle the stress and vibrations encountered in extreme conditions, making them more reliable for space missions.
The ARDITO Rover: A Platform for Future Planetary Missions
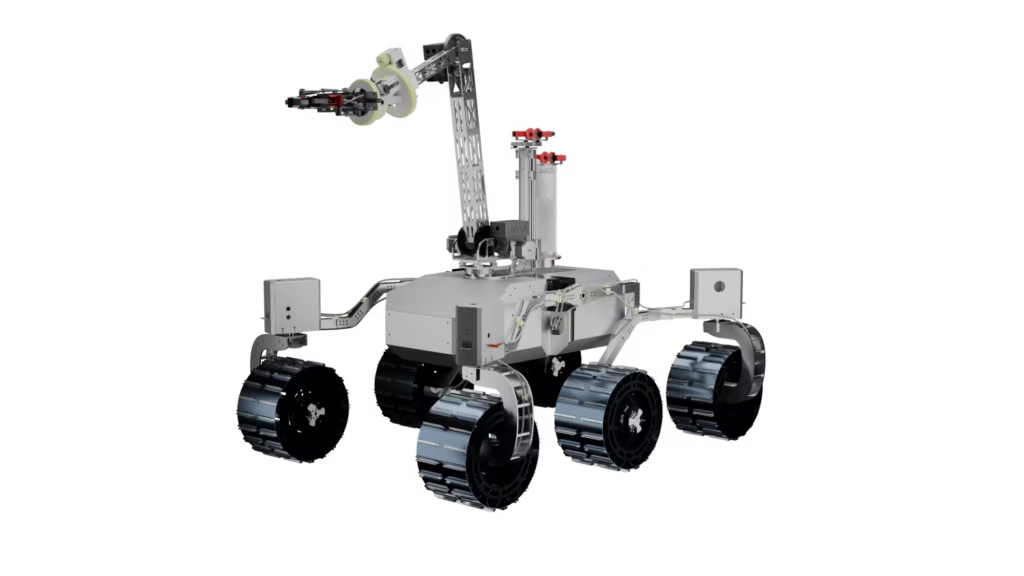
ARDITO is the latest of the space rovers developed by the DIANA team. Designed to support astronauts with mobility, sample collection, and environmental analysis. The rover features:
- A six-wheeled suspension system based on NASA’s rocker-bogie mechanism.
- A robotic arm with a sensorised claw for object manipulation.
- A soil sampling system to collect and analyse extra-terrestrial materials.
- Advanced stereo cameras and proprietary navigation algorithms for autonomous exploration.
One of the most innovative aspects of ARDITO is its airless wheels, engineered to adapt to the extreme conditions of Mars. Unlike traditional pneumatic wheels, these are designed to be resistant to punctures and provide exceptional traction. However, ensuring their longevity and performance required in-depth vibration and stress analysis.
Why Experimental Modal Analysis (EMA) Matters
Vibration and structural analysis play a crucial role in any high-performance engineering application. Whether in space exploration, Defence, automotive, or rail industries, understanding the natural frequencies of components is vital for preventing mechanical failure.
In ARDITO’s case, the elastic properties of its airless wheels made it essential to analyse their modal characteristics—essentially, how they naturally vibrate under different conditions. If not properly assessed, vibrations could lead to performance issues or premature wear.
To conduct the study, the DIANA team leveraged Dewesoft’s cutting-edge data acquisition and analysis tools:
- Dewesoft SIRIUSie-8xUNI+ – A high-performance data acquisition system for precise signal measurement.
- PCB 086C03 Modal Impact Hammer – Used to excite vibrations in the wheel.
- PCB 356BA43 Triaxial Shock Accelerometer – Captured response signals with high sensitivity.
- DewesoftX Software – Provided real-time analysis through its Modal Testing and Modal Analysis modules.
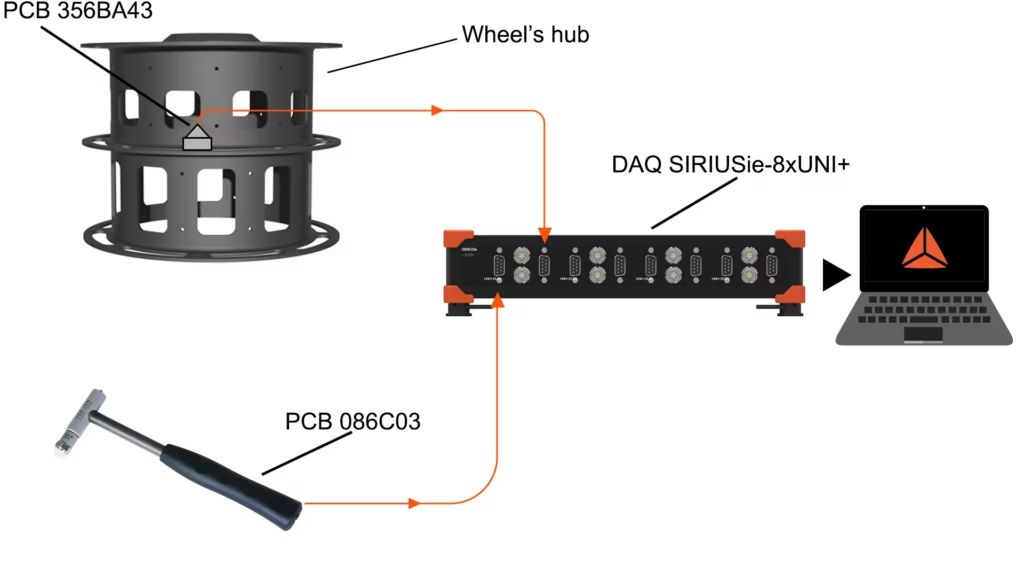
The Experimental Setup
The team set up a controlled test environment to measure and analyze the modal frequencies of the wheel hub. The wheel was placed on a polyurethane foam surface to simulate a free-free boundary condition, ensuring minimal external constraints.
Using an impact hammer and accelerometer, vibrations were introduced at 56 different measurement points. By analysing the resulting data in DewesoftX, the team identified critical resonance frequencies that could affect performance.
Key findings from the Mode Indicator Function (MIF) graph showed:
- Distinct resonance peaks in the 500-800 Hz and 1000-1500 Hz frequency ranges.
- A clear correlation between the experimental data and Finite Element Model (FEM) simulations, verifying the accuracy of the test results.
- The ability to fine-tune the wheel design to optimise durability and reliability.
Applications Beyond Space Robotics
While this study was done for a Martian rover, the principles of Experimental Modal Analysis used in various industries. Sectors that rely on high-performance structural components—including aerospace, Defence, mining, vehicle and rail—can benefit from similar testing methods
Dewesoft’s modal testing solutions used in:
- Defence and military applications – Analysing structural integrity of armoured vehicles and aircraft components.
- Mining and industrial machinery – Preventing resonance-induced failures in heavy equipment.
- Automotive and transportation – Enhancing vehicle durability through vibration testing.
- Rail infrastructure – Ensuring the longevity of tracks and rolling stock.
Conclusion: Pioneering Future Innovations with Dewesoft
The collaboration between the DIANA team and Dewesoft demonstrates how advanced data acquisition technology can drive innovation in even the most extreme environments. By leveraging EMA and Dewesoft’s high-precision instruments, engineers can ensure the reliability, safety, and efficiency of critical components.
At Metromatics, we proudly support Dewesoft solutions in Australia and New Zealand, bringing industry-leading data acquisition and vibration analysis tools to local engineers and researchers.
Interested in how Experimental Modal Analysis can enhance your industry applications? Contact us today to learn more about Dewesoft solutions or click to read the original article!