The article about the Load Cell used in Robotic Prosthesis has been supplied by our friends at FUTEK. We are proud to be their partner and supplier of their products to our customers in Australia and New Zealand. For more information on the Load Cell used, contact us.
For Matthew Carney of MIT Media Lab’s Biomechatronics group, the goal of building hyper-sophisticated machines is decidedly human. “At the most fundamental level we are trying to eliminate disability. We want to develop technologies that allow there to be no difference between disabled people, and someone of a normative body type,” says the biomechatronic engineer. He has designed a device that comes very close to doing that.
About the Robotic Prosthesis
Firstly, Carney’s PhD work for MIT is the revolutionary TF8 actuator, an untethered, lower-extremity powered-prostheses designed to replicate biological kinetic and kinematic function of ankles.The project has its origin in the powered prosthesis work pioneered by Dr. Hugh Herr and the team at the MIT Media Lab Biomechatronics Group (check out the video below to see how one of the engineers in that group has personalised the actuator for his own use).
This next-generation biomechatronic solution — which uses FUTEK’s LCM300 load cell for its force measurement — is built with a tightly integrating neurally-controlled power-dense actuator that allows it to be a nearly seamless replacement for a human limb. The device replicates natural human movement by combining walking data and optimised mechanical and electrical systems. But what really makes it novel is that it facilitates bi-directional communication between the body and the robot. This means that the amputated user experiences an artificial lower leg that not only functions, but also feels like a real one, as they can sense the robot’s movements and what it will do next.
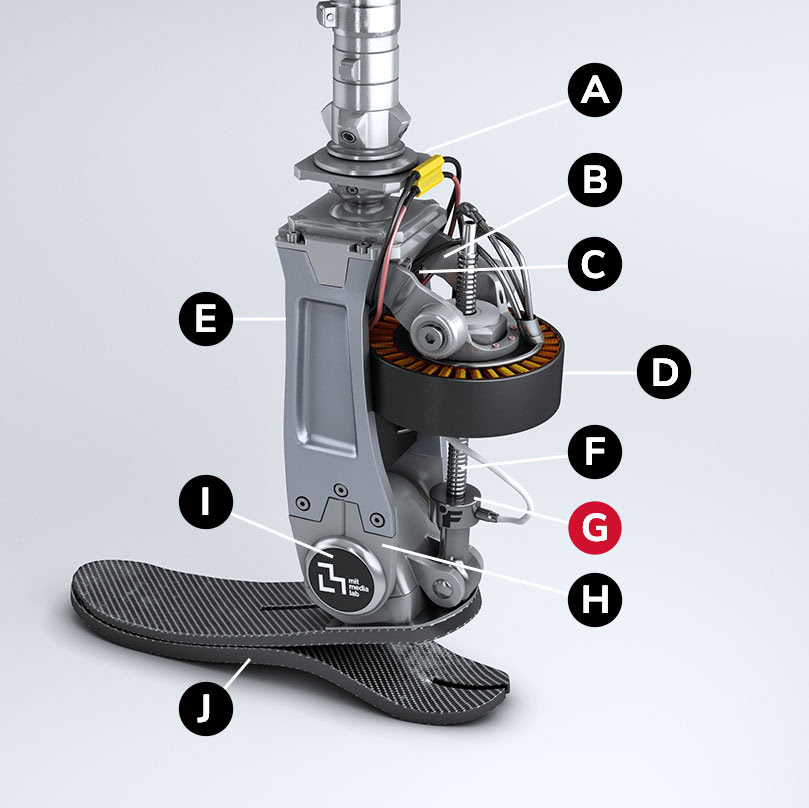
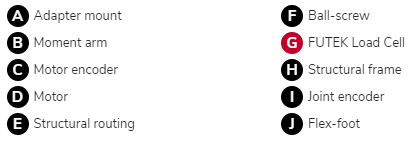
This interaction between human and machine is achieved through a new MIT-developed amputation technique. Firstly, that relocates the muscles above the amputation zone. Secondly, instead of cutting them off, allowing the brain, body and bionic device to interface in a way that is entirely unprecedented. Finally, FUTEK is humbled to contribute to this truly life-changing achievement.
About the load cell used in Robotic Prosthesis
The FUTEK Model LCM300 is a Inline Tension and Compression Miniature Load Cell built for Endurance, Press, or Inline applications. The standard LCM300 Threaded In Line Load Cell model has a very robust construction. Firstly, available in 17-4 Stainless Steel, with male threads on both ends. Plus a 3 Metre long 28 AWG 4 conductor shielded PVC cable. Options include models rated for higher temperatures or chemical resistant Teflon cable readily available. For a higher capacity range please see the LCM325, LCM350, or LCM375.
The LCM300 Miniature Load Cell has Nonlinearity of ±0.25% and Deflection of 0.001” [0.03 mm] nominal. The LCM300 Tension and Compression Load Cell can be customised to your requirements. Most models are available ex-stock, USA.
The LCM300 miniature force sensor was chosen for this application. Due to its small footprint, light weight, high accuracy and easy installation.