This case study on Dynamic Load Testing of Bridges was supplied by our friends at Dewesoft. It was originally written by Thomas Sturm Moreira the CEO of HochBau Engineering in Chile. Firstly, it is about how his Company HochBau was hired to do the dynamic measurements during load tests on two hanging bridges in Southern Chile. To read the original document, click here.
Summary of the Case Study.
In the region of Aysén in Southern Chile, the Southern Highway (Carretera Austral) provides one of the only connections from North to South. Therefore, it is essential that the bridges are structurally sound. Chile’s Ministry of Public works hires private companies to inspect and verify the designs of its engineering structures.
Dynamic measurements during load tests on two hanging bridges on the highway were required. Chile based HochBau Engineering was contracted to complete these tests. Some challenges existed. Such as the environmental conditions, the structural designs and time required for completion.
However, the Dewesoft IOLITE 3xMEMS-ACC offered a practical and cost-effective solution. These models are low noise, triaxial MEMS accelerometers. They carry data and power through one and the same ethernet cable completed the job.
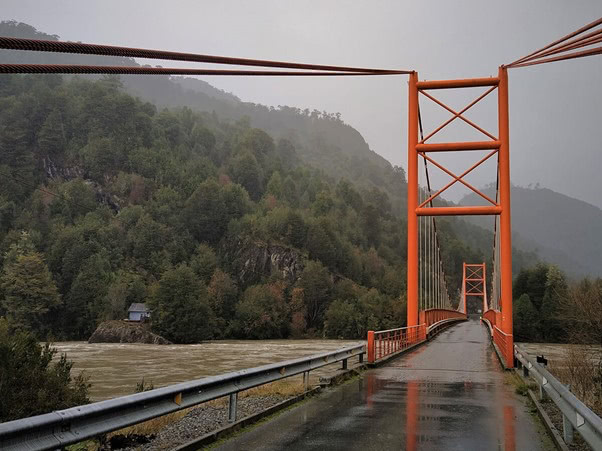
Finis Terrae – A Road To the End of the World
The Carretera Austral, which loosely translates as Southern Highway, is the backbone infrastructure of southern Chile’s Aysén region. Known for its spectacular landscapes and particularly harsh climate. It’s a major tourist attraction for international and local adventurers.
The highway runs south from Puerto Montt to Villa O’Higgins for about 1,240 kilometres, passing through rural Patagonia. These areas are sparsely populated. However, without the Carretera, its residents wouldn’t have land connectivity with the north of the country.
Furthermore, its eventful rugged geography and large rivers. Actually, bring water all year round. Therefore, forcing the Carretera to have large hanging or suspension bridges over rivers and ferries in the larger fjords.
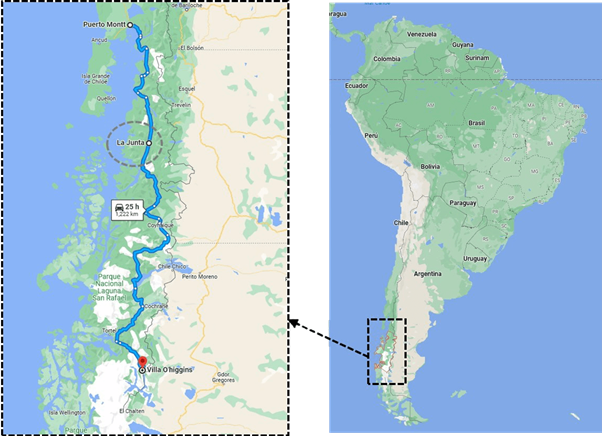
Figure 1. Location of the Carretera Austral (Google Maps).
Most of the infrastructure of the Carretera Austral was built or enlarged in the 1990s. Hence, thorough inspection and analysis were due.
To assess the current condition of the main hanging bridges of the Aysén region, the Ministry of Public Works (MOP) is hiring private companies, through public biddings, to inspect, test, and verify their designs.
Under this scheme, MOP entrusted the large road construction company R&Q with the assessment of the Palena and Rosselot bridges close to the town of La Junta. In turn, R&Q hired COWI for the structural design assessment, MRH for the inspection, and HochBau for the dynamic measurements during load tests.
The Hanging Bridges
The Palena and Rosselot are suspension bridges. With free long spans of 150 m and 130 m respectively. They have two metallic towers, which support the cables. Their reinforced concrete bridge decks are supported by vertical rods which hang from the main cables. The decks are stiffened by two 2,1 m high lateral metallic trusses.
The inspection works discovered several fractures near connections of the stiffener trusses and several other defects. Furthermore, unlike most hanging bridges, the decks have several expansion joints along their span, which are uneven and their edges are worn-out.
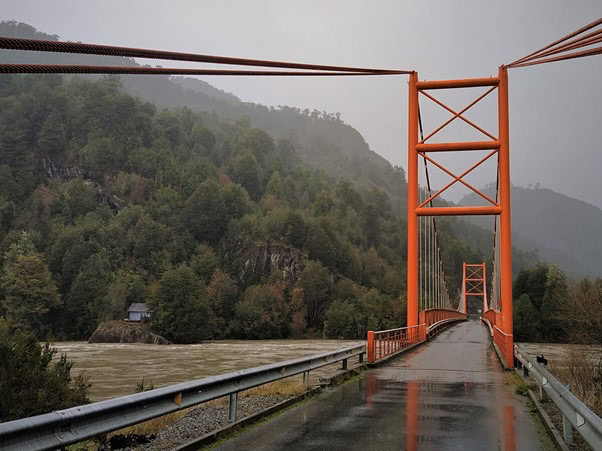
Figure 2. The Palena Bridge.
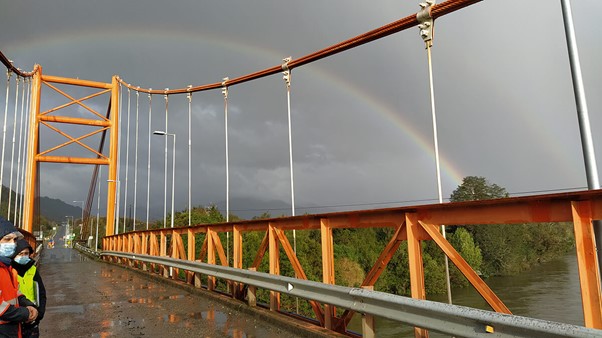
Figure 3. The Rosselot Bridge.
Firstly, as part of the load tests which were carried out. HochBau was hired to measure the dynamic response of the bridges. The load tests were carried out with a 23-ton three axle load truck.
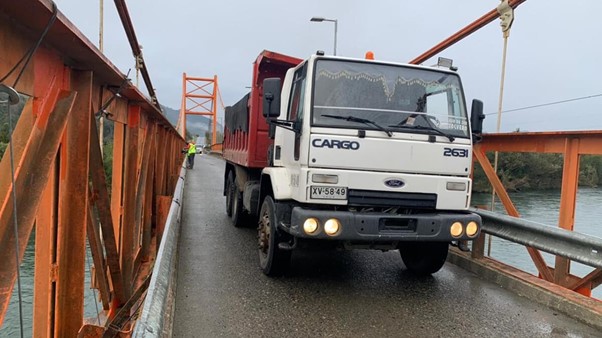
Figure 4. A three-axle load truck on the Rosselot Bridge.
Three load tests were defined:
- Static Load Test: The truck is parked at ¼, ½, and ¾ of the bridge span, and the deflection of the bridges is measured with an engineering level.
- Dynamic Load Test: The truck passes the bridge in both directions at 5 km/h, 15 km/h, and 25 km/h while dynamic measurements are made. The dynamic response is recorded during these tests.
- Ambient Vibration Measurements: The responses of the bridges are recorded under ambient excitation (wind, river, low traffic, etc.). The results are used to determine the natural frequencies and mode shapes (OMA).
Hurdles – Working in the Rain
Secondly, the measurements during the Dynamic Load Tests and the Ambient Vibration Measurements were carried out by HochBau.
Decisions made with the client that a total of six points of acceleration measurement would be used. At both sides of ¼, ½, and ¾ of the span of the bridges. This meant the vertical and transversal directions had to be measured in all points. As well as the longitudinal direction in at least 2 points, making up already at least 14 channels.
Several hurdles had to be overcome for the success of this endeavour, mainly:
- Geographic location: La junta is 1415 km from Santiago, Chile’s capital. All measurement systems, tools, and all supplies had to be taken by car there. Meticulous planning was needed; if anything stayed behind, they would not be able to get it in Aysén.
- Little upfront time: Delivery of hardware takes its time. Delivery in midst of a pandemic and a chip and aluminium bar shortage takes even more time. Having only two months from notice to execution of on-site works of the project, time was tight.
- Flexible structure: On the technical side, a decision of which sensor technology to use had to be made; Piezoelectric, MEMs, or Force Balance? Despite not knowing the bridges’ lowest natural frequencies, intuition dictated that they had to be well under 1 Hz.
- Bridge length: The bridges have no berm. Therefore, no place on the structure for a person to record and monitor the measurements. The length of the bridges meant long cables. If analog cables would be used, the DAQs would have to be brought closer to the sensors, since the shortest cable might have been over 40 m.
- Installation time: The measurement system had to be installed and ready to measure on the same day as the load tests would take place. Pre-installing the system was not an option. Due to theft possibilities.
- The Weather!!!: Chile is known as a largely dry country; it even hosts the driest desert on the planet. But despite this, the Aysén region competes with some of the rainiest regions of the world. Even though it rains all year round, the tests were carried out in July. This was at the height of South America’s winter. Buckets of water falling from the sky and near-freezing temperatures were guaranteed.
Suited for Rough Conditions
Keeping all the beforementioned aspects into account. Decisions made – both practical and technical. The accelerometers had to have a DC component (i.e., 0 Hz). This was due to the low frequencies to be measured. Therefore, piezoelectric sensors were discarded as an option.
Between MEMS and Force Balance sensors. Force Balance offers a much higher dynamic range. However, more ideal for measuring a very tall or base-isolated building. Nevertheless, for the dynamic tests, both are suited. But would the signal-to-noise ratio be enough for ambient vibration measurements?
For this campaign, HochBau knew that the external ambient excitation would be large enough. Even for the 90 dB dynamic range of MEMs. However, the next issue was the cabling. If analog sensors were used, the DAQs had to get close to the sensors. But having 14 cables between 45 m and 105 m in length was not an option. This is because of the cost and additional noise the cables would infer into the measured signals.
Piezoelectric (IEPE) | Force Balance | MEMS | |
Low Freq Response | Acceptable | Excellent | Excellent |
High Freq Response | High | Low | Acceptable |
Transducer Cost | Acceptable | High | Low |
Dynamic Range | Good | Excellent | Acceptable |
Wiring Cost | Acceptable | Acceptable | Excellent |
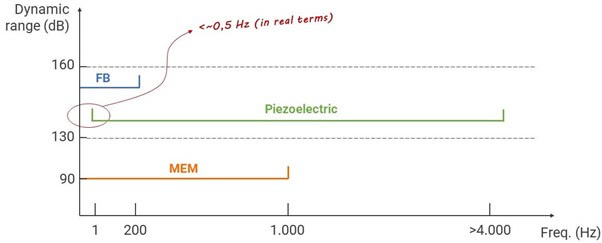
Figure 5. Illustration of the typical dynamic ranges of different accelerometer technologies.
Product chosen
Luckily, a practical cost-effective measurement solution was at hand. The IOLITE 3xMEMS-ACC combines a low-noise triaxial MEMS accelerometer and an ADC module (i.e. local DAQ) into one single relatively small piece of equipment.
Since the measured quantities are digitised in the sensor. The results are queried digitally through the EtherCAT protocol via ethernet cables (CAT5e or CAT6).
The EtherCAT protocol has the advantage of time inherent synchronisation between all sensors. It also allows connection to the sensors in series or, with a Beckhoff EtherCAT switch, in branches. Additionally, the sensors support Power Over Ethernet (PoE). This allows power to the sensor through the same cable carrying the queried data. Meaning no power is required over long cables to every sensor.
The added advantage was that they could be bought in an IP67 aluminium housing! However, to be watertight, the network cable had to be passed through the waterproof cable glands. Before crimping the RJ45 connector and then the aluminium housing cover could be closed.
Remember the delivery/supply chain issue? Dewesoft’s fabrication and delivery time, on such short notice, only allowed for the delivery of three waterproof MEMs. Luckily, HochBau’s local provider Varitec leased them three indoor MEMs.
Two issues remaining:
- how to waterproof the three indoor MEMs and
- how to avoid the on-site opening and crimping of the ethernet cables of the three waterproof MEMs?
The latter would also have taken a long while on-site! In the end, wrapping the indoor MEMS in plastic foil and preinstalling 30 cm ethernet cables to the waterproof MEMs worked
The connection with the longer cables was then made through RJ45 couplers. Due to the roughness of the concrete deck, the MEMS were fastened to thick steel plates which were bolted to the bridge deck.
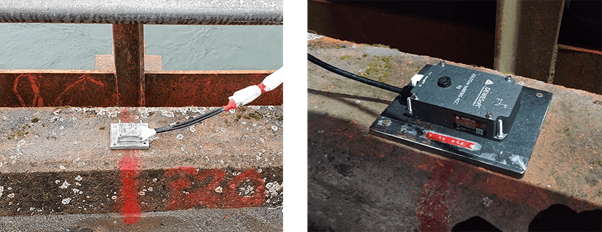
Figure 6. Installed MEMS accelerometers, indoor version left, waterproof version right.
With all this said, only the system layout was missing. Together with the Technical Support Area of Varitec, a chain architecture, over a 250 m CAT6 line was chosen over a branch architecture. Since only one PoE and no EtherCAT switch would be necessary this way.
Figure 7 below sensor location and how the cables were laid out, using the Palena Bridge as an example.
The cable was crossed from the third to the fourth MEM through the expansion joints. The measurement software had to reside on a notebook in a dry and safe location. So a car (SUV) was parked close to the entrances of the bridges (control station) from where the system was also powered using a gasoline mobile generator.
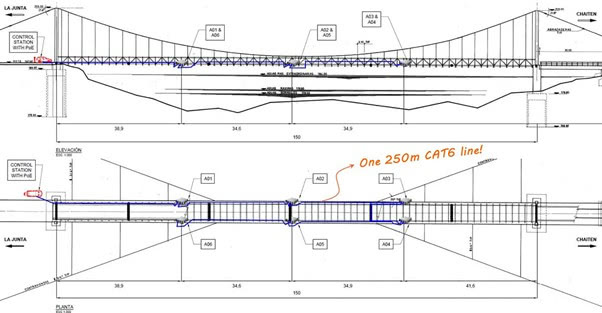
Figure 7. System layout, Palena Bridge.
However, from the car, the measurement engineer would have no visibility off the deck of the bridge. He would be working blindly without seeing the passing of the truck. Relying purely on radio communication. Therefore, a USB webcam was placed at the entrances of the bridges and integrated into the DewesoftX environment. The 15 m distance to the bridges resulted in an USB over Ethernet extender.
The Issues and Measurement Results
As mentioned before, measurements of the moving truck at different speeds and ambient vibration measurements were made.
The measurements during the dynamic load tests showed that the RMS values of the response of the bridges increase linearly with speed. They are largest in the vertical direction (around 0.01 g at 25 km/h). Nevertheless, it can also be observed that there are always several impacts whilst the truck is passing. Independently of speed, with crest factors of up to 14, reaching up to 0.15 g in the vertical direction and 0.06 g in the lateral direction.
It was concluded, impacts were the result of the uneven and worn-out expansion joints.

Figure 8. Monitoring the dynamic load tests (left) and dashboard used during measurements (right).
With the records of the ambient vibration, the natural frequencies and mode shapes of the bridges were determined. The Palena bridge is used as an example, see figures 9-11. The first horizontal mode was lower than predicted by the structural finite element model. But this was expected when accounting for structural deficiencies which were identified during the visual inspection.
Furthermore, the first three vertical modes were identified. Results were valuable for the structural engineers. They will be used to calibrate their finite element models for further analysis and assessment of possible retrofit options.
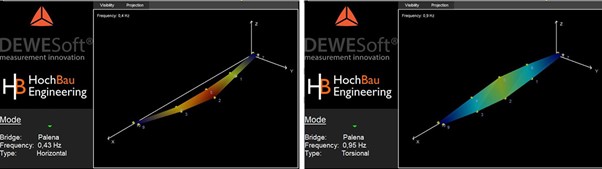
Figure 9. Horizontal (left) and torsional (right) modes of the Palena Bridge.
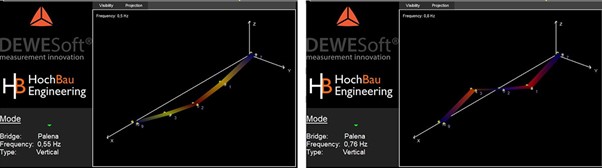
Figure 10. First (left) and second (right) vertical modes of the Palena Bridge.
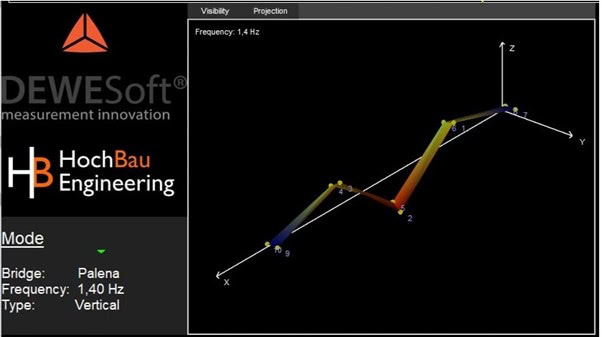
Figure 11. Third vertical mode of the Palena Bridge.
Conclusion
Wrapping it up, measurement campaigns can differ greatly depending on the location. As soon as heavy rain in remote locations factors in. All details of the system architecture and logistics need even greater care.
The dynamic measurements of the load tests with the truck gave valuable input to the structural engineers assessing the current condition of the suspension bridges. The retrofitting proposals will be assessed. With a calibrated finite element model. Rather than just a theoretical one, thanks to the acquired data.
Finally, this field campaign highlights the importance of monitoring bridges and other critical infrastructure. With the decreasing cost of technology and increasing connectivity, even in remote locations we’re aiming at the design of continuous and permanent Structural Health Monitoring Systems (SHM) for the bridges of today and tomorrow.
PS: An expanded system conducted. However, using temperature and strain gauge. For measurements on two other hanging bridges, further down in Patagonia.