This article on how Dewesoft Data Acquisition is fine tuning the perfect BBQ was kindly provided by our friends at Dewesoft. For the original article, click here.
BBQ-ing is a “thing”. It is often a passion. The satisfaction of delivering the perfect steaks, lamb chops and sausages to friends and family leads us on the hunt for a BBQ or Grill that delivers. US based Traeger Grills is the market leader in wood pellet grills and have been using Dewesoft Data Acquisition Systems to fine tune the BBQ Science in delivering the perfect BBQ.
About Traeger Grills
Traeger Grills are on a quest to create the best BBQ on the market. Firstly, do you want to know the reasons why wooden pellet grills consistently create delicious masterpieces? The “secret sauce” is the quality controlled hardwood pellets combined with the advanced control system.
An advanced controller?
Yes, an advanced controller! Ever heard of a PID loop/controllers?
A PID is a Proportional Integral Derivative Controller. It uses a feedback loop to control a device. So, the operator sets a “wanted” temperature and the grill much reach and then maintain it. This is in despite of variety of constantly varying conditions.
So how does DAQ fit into BBQ manufacturing? It’s all in the product testing, baby…..
Before data acquisition was invented, product testing was subjective. For example, when car companies tested their cars on tracks, they relied on the opinions of drivers. Who provided feed back how different modifications to the suspension or shock absorbers affected comfort and drivability.
However, today it is essential to make objective, repeatable measurements and this is achieved by data acquisition (DAQ) instruments.
So, Traeger engineers reached out to the DAQ experts at Dewesoft. Dewesoft was able to help them measure and collect data with Dewesoft instruments in their test labs. Parameters included temperature, command points and CAN-Bus data. This information was provided to the Traeger Engineers. Who were easily able to evaluate the performance and effects of any modifications or tweaks that they made to the controls platform.
The Auger Example
As an example, there is an auger. It turns and feeds wood pellets into the fire pot based on a timed schedule set by the grill controller. The question was asked how fast should it turn? Every variable must be controlled in real-time to achieve the perfect cooking conditions as selected by the operator:
Such as
- Flame intensity
- Auger condition/speed
- Fan condition/speed
- “Hot rod” pellet igniter condition
- Door position
The PID controller takes the “wanted” temperature and compares it to the “feedback,” which is gathered from sensors in the grill. This might sound simple, but it’s not. Why?
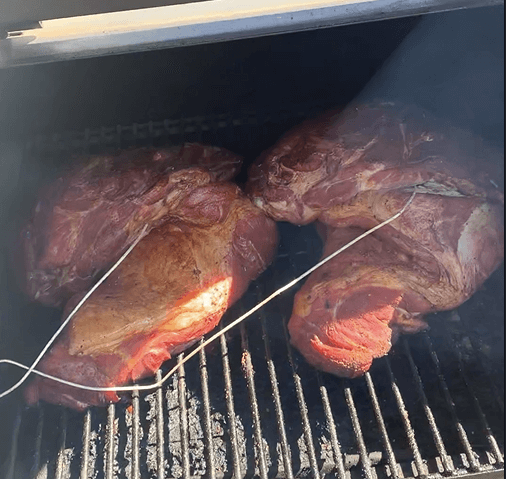
Figure 1. Several cuts of meat are instrumented with temperature sensors that output their internal temperatures to the Dewesoft DAQ system.
Traeger use precisely tuned coefficients. Therefore, various parameters are continually adjusted to achieve the wanted temperature. But there are PID loops for the auger. Plus, another for the fan speeds, etc. The coefficients in the PID loops will change when conditions change. Such as when the door is open, how much wind there is, when the ambient temperature changes, and more. Nested PID controls and constantly changing control coefficients are no small engineering feat.
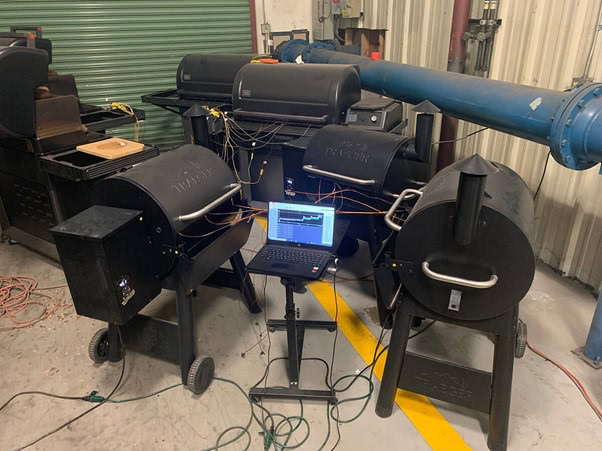
Measurement Procedure and Setup
The product used was the Dewesoft KRYPTON DAQ Modules. This was because of their wide temperature operating range. Multiple KRYPTON-TH modules were paired with Dewesoft CAN Interfaces. This allowed analog response data to be recorded at the same time with the CAN command data.
The other advantage KRYPTON Modules are rugged. The are a seal module against water, smoke, dust and even the stickiest BBQ sauce.
The modules are daisy chained using a single EtherCAT cable. The cable carries power, digitised data, and module to module synchronisation. KRYPTON (and CAN) modules can be placed right where they are needed. Therefore, allowing sensitive analog sensor lines as short as possible.
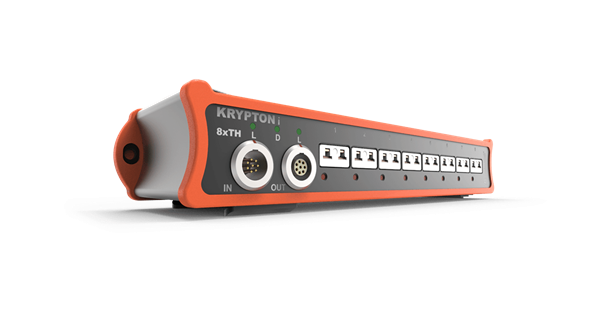
Figure 3. KRYPTON 8xTH module with 8 isolated universal thermocouple inputs.
In addition to dozens of command data parameters coming across the CAN BUS, a typical test includes more than 32 channels of thermocouple analog inputs. As well as 600+ additional math channels. These channels are calculated in real-time. Therefore, validating criteria for immediate responses and feedback to changes in their control system.
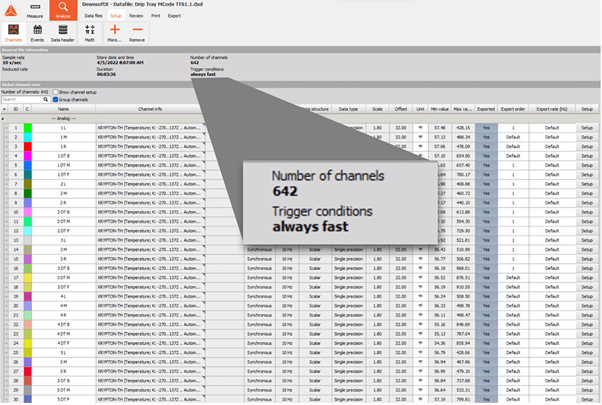
Figure 4. Channel setup screen. 642 channels were acquired simultaneously.
Dewesoft’s DAQ system can be scaled from testing a single grill to testing multiple grills simultaneously. This flexibility also represents a huge efficiency boost. Turning a previously serial process into a parallel one. Because they are so easily daisy-chained, KRYPTON modules can be added or removed as required to satisfy the required number of channels. Dewesoft X software automatically adjusts to the modules that are connected.
Flexible, User-configurable Displays
Traeger engineers took advantage of Dewesoft X’s multiple display capability to create a screen for each grill under test. So the display shows the key parameters that need to be seen during the test. Traeger decided to make a separate display for each grill. This allowed them to easily choose amongst them during the test. Otherwise, multiple monitors can be connected and a screen could have been placed on each one.
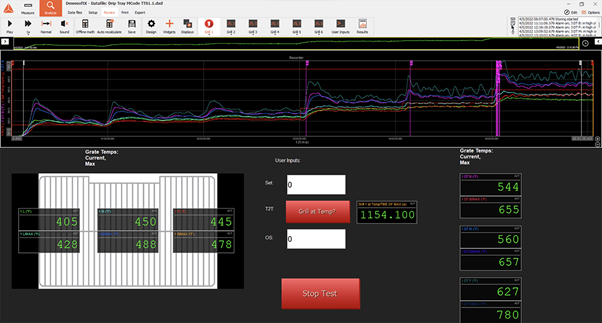
Figure 5. This display shows the parameters that must be observed during the test.
Traeger positioned user input fields plus the convenient STOP TEST button in the centre of the screen. As well as a strip chart display running left to right across the top of the display.
If a touchscreen is used, buttons can be pressed with your finger. Otherwise, a mouse and keyboard can be used to click buttons and interact with anything on the screen. All interactive and display elements are completely user-configurable within Dewesoft X software.
Other Display Ideas
Notice the image of the grilling grate, with digital temperature values shown above it where the thermocouple sensors are located. Video can also be used if needed, to see the test, for example, to watch the movement of an auger, or the position of a door, just to name a few examples.
Traeger engineers use another custom display to compare the results and summarise the performance of all grills under test. The historical performance for each setpoint is easily compared with how the grill responded to the R&D’s design modifications.
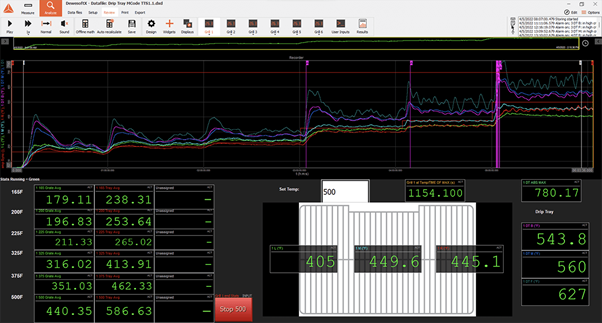
Figure 6. Custom display comparing six grills simultaneously.
They also created another display to allow engineers to enter all their inputs and set points in one place. This allowed them to save time whilst grills are testing simultaneously. With the Dewesoft X Software there is not limit to the number of displays and entire setups that can be created.
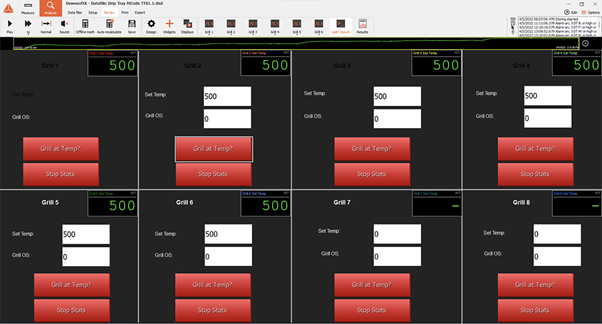
Figure 7. Custom display for entering all inputs and set-points in one place.
Real-time and Off-line Mathematics
The Dewesoft X Software contains a real time maths engine. All parameters can be calculated and displayed in real-time. This saves the Traeger engineers countless hours. It also speeds up the R&D Process. As the engineers don’t have to wait until the tests are completed to process the results. The results are calculated and displayed and saved in real time.
The software also supports recalculation and the addition of additional maths functions after recording. Dewesoft X can export data to a range of popular data analysis formats. Therefore, there is not limit to what can be done in post processing.
Testing in real-world conditions
Running tests in a temperature controlled environment is necessary for evaluating aspects of controller modifications. However, Traeger realises that their grills will be used in the sun, wind, and rain and across a whole range of weather conditions.
Traeger are based in Salt Lake City which is located at a high altitude of 1,288 metres. So the engineers are familiar with the snow, ice, howling winds and temperature extremes. They also know that a dedicated BBQ chef will not let a little crazy weather stop them from cooking. So the grills have to be tested under all conditions and across a wide range of ambient temperatures.
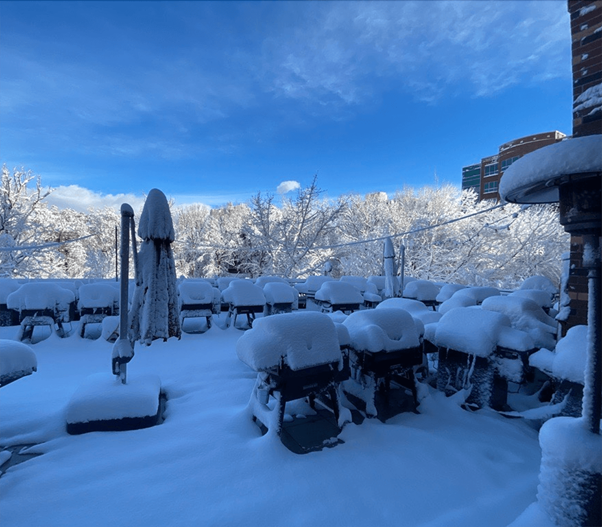
Figure 8. Setting up winter testing of multiple Traeger Grills
Summary and Conclusion
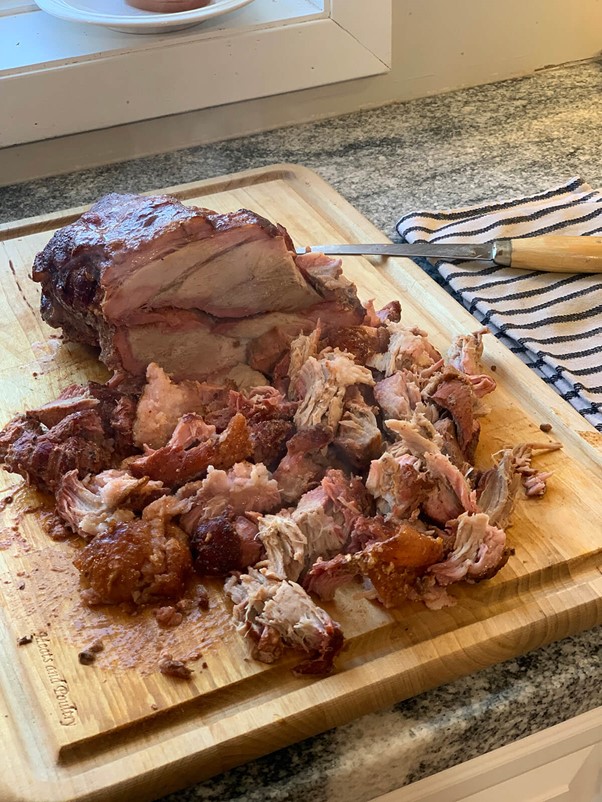
Figure 9. The “End Product”
Whether you are a BBQ connoisseur, a backyard grill master, or someone who simply loves to sink their teeth into a tender, fall-off-the-bone beef rib, Dewesoft and Traeger hope you have gained a better appreciation of the technology and testing that goes into making these high-tech grills.
At Dewesoft, they were happy to work with such an innovative engineering team. After all of the testing, there was plenty of delicious BBQ to go around. In the spirit of conservation, Dewesoft sales engineers did not let any of it go to waste.
In conclusion, to learn more about data acquisition fine tuning the perfect BBQ, contact us.